Preparing
Surface preparation
Why prepare a surface?
Any metal surface must first be well prepared prior to be coated to ensure optimum resistance of the coating and achieve desired project life.
Many specifications could help you determine the required preparation, and these include, but are not limited to, substrate to be coated (aluminum, steel, concrete…), the coating composition (paint, rubber, metallization, etc.) the aesthetic desired, the environment and all other requirements.
The main ones are:
- SSPC (The Society of Protective Coatings): they create standards for coatings that protect and preserve concrete, steel and other industrial & marine structures and surfaces.
- NACE (The National Association of Corrosion Engineers): standards applied to corrosion prevention and control in industries during the design, building and operation to limit the impact of corrosion.
- ISO: Standards in Corrosion Protection. They have a volume that has more than 225 ISO International Standards that covers the best methods of performance of paints and varnishes of steel substrates:
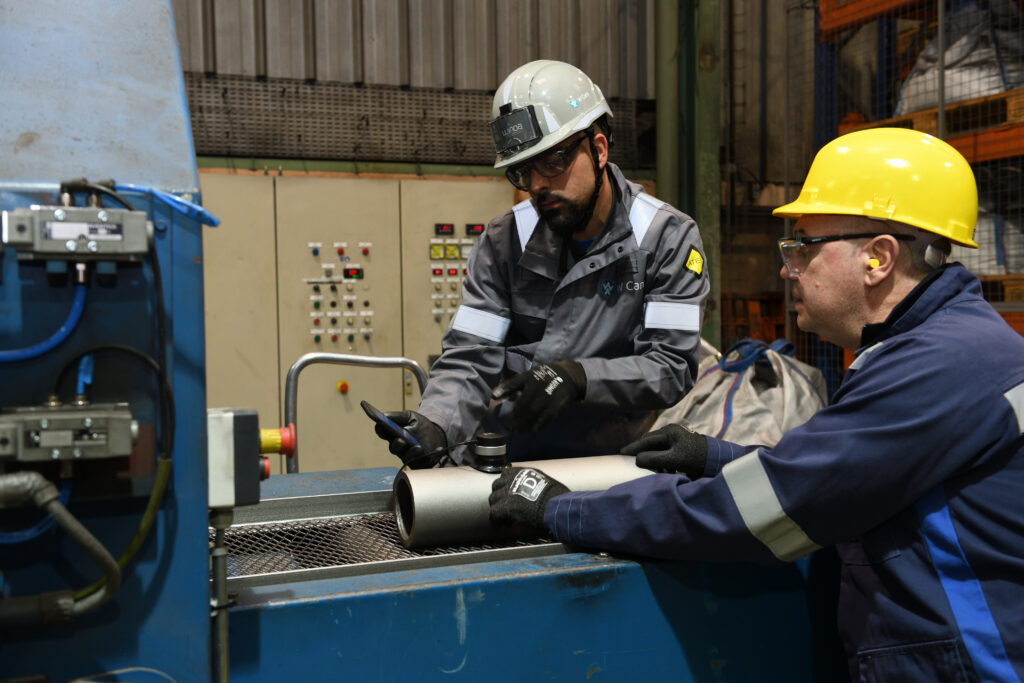
Applications
Preparing
For surface preparation applications, it is first necessary to define the initial state of the surface, the desired state, the characteristics required of the surfaces and the equipment used for the realization. We can help you define them, but the main ones are:
- Initial state: See specification SSPC VIS 1: guide that describes with the use of photographs the initial surface states.
- Practically no rust
- Rust spots
- Cavities
- Uniform rust
- Desired state: several standard degrees of preparation exists, selected primarily depending on the application, durability, and environment. The main 4 standard levels seen in the ISO 8501 (Link) or SSPC VIS 1 are:
- SA3 – SP5 – White metal – Blast-cleaning to visually clean steel (99%)
- SA 2.5 – SP10 – Near white – Very through blast cleaning (96%)
- SA 2 – SP6 – Commercial – Thorough blast cleaning (80%)
- SA 1 – SP 7 – Brush off – Light cleaning by brush.
Note: cleanliness is expressed as “the degree of cleanliness of an initial surface state”. Ex: The degree of cleanliness SA2.5 on a sheet of steel, whose initial state was C, is C SA2.5”
Characteristics required
Roughness
Among others, roughness is one characteristic to control for any surface preparation application. We have training and tools to help you measure and control these parameters. The shape of the surface (peaks and valleys (troughs)) can be expressed using:
- Rmax: Maximum height between a trough and a peak. It quantifies the maximum height to be covered by a coating.
- Rz: Average of maximum heights of a consecutive segment, in the assessment length.
- Ra: Arithmetic average of all the profile’s deviations.
- Peaks count: number of peaks per length unit enables evaluation of the average width and density of the peaks, which are elements of prime importance in coating adhesion.
- Rsk (degree of skew / symmetry) and Rku (kurtosis / sharpness) are also important factors in coating applications.
Most suitable products
Our product ranges
For surface preparation of steel, concrete, aluminum or other, a complete range of blasting abrasives exist. Whether mineral or manufactured, they each have their characteristics and advantages. One of the first selection criteria is the equipment used:
Shot blast wheels
Our products range for wheel blast machines
Commonly called “Wheelabrator”, wheel blasters have the advantage of recycling, cleaning, and propelling large quantities of abrasive media. However, a full range of media are not suitable for it, including those with a low recyclability rate, except for very specific applications:
Air blast applications
ours products for air blast applications
Whether automated for large-scale projects (railroad, windmills), or for open air application (construction), or in blast chambers fully equipped with a recycling system (Industrial sandblasting), airblasting (commonly referred as sandblasting) is a common process that uses compressed air to propel abrasive media across the surface of your parts. To select the optimal airblast abrasive for your application, we invite you to contact our technical team. Here are the main ones:
Contact us
To be able to select the best option for your surface preparation application, please communicate with one of our specialists